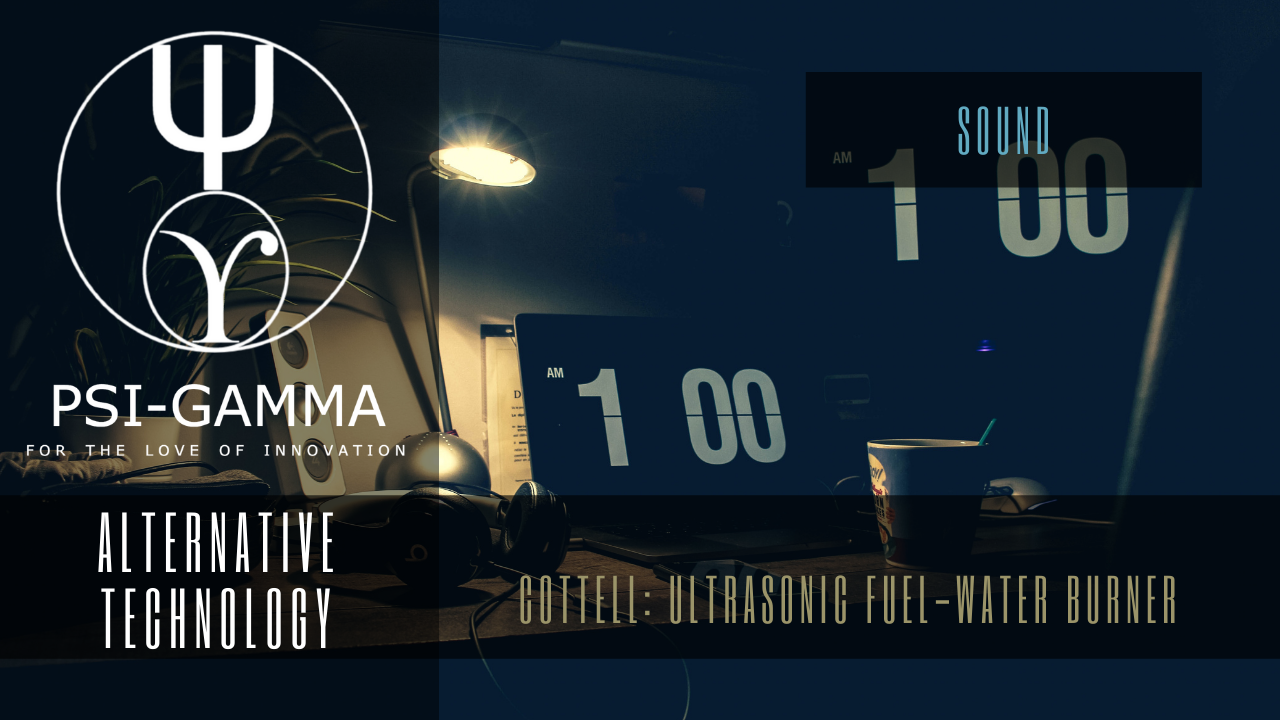
A Solution to Air Pollution
In the wake of the energy-crisis a 50-year-old British-born inventor named Eric Cottell has come up with an ingeniously simple and economically practical solution — one that is now exciting industry and government officials alike.
In the conventional combustion process, fuel is combined with air and turned. The result is carbon dioxide, water vapor and heavy oxides of nitrogen, which are a prime cause of chemical smog. Cottell reasoned that if water could largely replace air as a source of oxygen in combustion, this would avoid the large amounts of nitrogen introduced by the air — and thus eliminate much of the noxious nitrogen oxides.
To accomplish this, he turned to a device he had patented 22 years ago — an ultrasonic reactor that emulsifies heavy liquids and is widely used today to prepare such products as Worcestershire sauce, ketchup, cosmetics and paint. By refining the reactor, Cottell was able to break water into particles about one fifty-thousandth of an inch in diameter and to disperse them evenly in oil (or gasoline) to create an emulsion that was 70 percent oil and 30 percent water. When this emulsion was burned, Cottell found :
(1) that there were far fewer waste products and
(2) that the small water droplets expand on heating, then explode into steam, in turn shattering the oil into even finer particles, and thus increasing the surface area of the fuel exposed for burning.
Last month Cottell divided his time between Washington, in talks with officials of the Federal Energy Office, and Detroit, where he consulted with engineers working to meet the tight 1976 automobile-emission requirements. So far, auto tests have shown that with an ultrasonic reactor attached to a carburetor, a car can get almost DOUBLE the normal miles per gallon of gasolinge — with neglible exhausts. Cottell’s company, Tymponic Corp. of Long Island, N.Y., is also about to produce units for home oil burners that will be no larger than a flashlight and cost $100 to $150.
Last winter, two Long Island schools converted to Cottell’s system, and both reduced their fuel usage by about 25%. Adelphi University reports that it saved more than 3,500 gallons of oil per week! — and reduced soot output by 98 %.”
Popular Mechanics (November 1972)
“A Furnace That ‘Burns’ Water”
by John F. Pearson
A revolutionary combustion system makes it possible to ‘burn’ emulsions of fuel and water. It works in a car engine as well as an oil furnace – and cuts pollutants, too.
It’s impossible. An oil burner simply can’t run on a fuel that is one-third water — tap water, at that. But I recently saw it done.
The demonstration was at the Bayville, NY home of Eric C. Cottell, a British-born engineer and inventor. The gadget that made the “impossible” happen is a Cottell invention called the Ultrasonic Reactor — a device resembling a long, slim electric motor. It contains a crystal stack at one end and a mixing chamber at the other.
When a 60-cycle current is applied, the crystals vibrate at 20,000 cycles per second, turning the reactor into a “super-blender”. As shown in the diagram, oil and water (70% oil, 30% water) flow into the reactor, where a terrific vibrating force causes water and oil molecules to rupture. The two liquids form an emulsion in which tiny particles of water are dispersed throughout the oil. When this happens, says the inventor, the surface area of the water is increased millions of times. Thus, when the emulsion hits the furnace’s combustion chamber, the water “explodes” into superheated steam, adding to the energy ouput of the oil.
In hundreds of tests of his system, Cottell has found that ordinary boilers run at efficiencies close to 100% — as astounding result that neither he nor leading combustion experts can explain. In the demonstration I saw, gauges indicated that the emulsion produced the same amount of heat as a 100% oil fuel.
In addition to stretching fuel, the system reportedly produces fewer pollutants than standard oil combustion. The fact that one-third less oil is burned is a key anti-pollution factor.
Though Cottell sees many potential applications for the reactor — in auto, ship and plane engines, for example — he thinks the best immediate application is in heating plants of large apartment buildings.
“This is by far my most exciting invention”, says Cottell, who holds patents in the fields of ultrasonics, hydraulics, and chemistry.
US Patent # 3, 749,318
Combustion Method and Apparatus Burning an Intimate Emulsion of Fuel and Water
Abstract — A combustion apparatus and process in which a water-in-oil emulsion of liquid fuel, such as liquid hydrocarbons, containing from 10 to 50 % water, the emulsion being produced without any substantial emulsifying agent and preferably by sonic agitation, is burned.
The combustion of liquid fuel, such as liquid hydrocarbons, is a standard method of power and/or heat generation. The combustion may be in a system where the heat is transferred to another medium, such as water, with or without boiling the water, or the fuel may be burned in various types of internal combustion engines, such as those operating on Otto, diesel, or other cycle. The amount of oxygen, usually air, is at least about theoretically sufficient for complete combustion of the fuel elements.
Considerable problems have arisen. If there is a very large excess of oxygen, the efficiency of the combustion process is lowered because a considerable amount of the air, including inert nitrogen, has to be heated up. In the case of an internal combustion engine, operating with excessive amounts of oxygen can result in slow combustion, which can overheat and burn out exhaust valves. If the combustion is with amounts of oxygen and fuel more nearly in balance, for example with only a small excess of oxygen, problems arise with incomplete combustion. This can result in excessive amount of carbon monoxide and/or incompletely burned fuel, which may show up as unburned hydrocarbons, soot and the like. Incomplete combustion lowers the combustion efficiency and can also contaminate the equipment. In the case of internal combustion engines, unburned hydrocarbons, carbon monoxide, and oxides of nitrogen, generally symbolized by the formula NOx, are serious atmospheric pollutants as they give rise to photochemical smog and the like. Contamination of NOx from an IC engine usually results when combustion temperature is high.
It has been proposed in the past to introduce streams of water into a burner or to inject water into an internal combustion engine as it operates. This has proven to reduce somewhat incompletely burned fuel deposited in the form of carbon, and in the case of IC engines this can lower NOx production and also in certain cases, such as aircraft piston engines, permit operating for short times at higher power outputs with very rich mixtures which would otherwise burn up the engine. Water injection, however, has serious drawbacks. In the first place, it is very difficult to control relative amounts of water and fuel precisely. Even if the control is maintained to a satisfactory degree, efficiency drops because the water has to be vaporized, with its extremely high latent heat, and heated up in the combustion, which takes further power because of the high specific heat of water vapor. As a result, water injection has only bee practically used in unusual circumstances.
Summary of the Invention
The present invention burns an extremely fine emulsion of water and liquid fuel, normally hydrocarbonaceous fuel, in which the water droplets are dispersed in an extremely fine average particle size. While the present invention is not absolutely limited to the method by which the emulsion is carried out, it is preferred to emulsify by using an ultrasonic probe or other device which agitates the fuel and water to produce an extraordinarily finely dispersed emulsion, because it is the fine dispersion that produces the important new results which will be set out below; mere presence of the water does not.
According to the present invention, if a very fine emulsion is burned, which may have from about 10% to as much as 50% water, extremely clean combustion results, contamination and pollution are minimized, and in a straight atmospheric burner up to 30% of water will give results in which the heat obtained by the combustion is substantially the same as if all hydrocarbon fuel were burned. In other words, with 70% fuel and 30% water, the emulsion will produce the same amount of heating. This surprising result has been repeatedly tested, and while I do not want to limit the present invention to any particular theory, it seems probable that the combustion of the emulsion is so complete that the smaller amount of fuel is completely burned and the same final heat is obtained as if there were no water present. The above statements are made with respect to a system in which the surfaces which are heated are at a sufficiently high temperature so that water vapor does not condense. In other words, no part of the new result is due to condensation of water vapor on cooler surfaces. In the case of the application to an IC engine, not only are the surfaces hot but the exhaust gases leave the engine cylinder greatly above the condensation point of water vapor.
In the IC engine modification of the present invention, while the total amount of power may be as great or, under certain circumstances, even greater, the peak flame temperature is usually lower, and it seems probable that the reduced emission of NOx results primarily from this factor. However, this is not known, and the water vapor present in larger amounts as compared to carbon dioxide may also play a part. Therefore, it is not intended to limit the invention to any particular theory, and the above statements are made because I think the factors mentioned are at least some, and conceivably the only, factors involved.
The invention is not limited to the time in the whole operation when the very fine water-in-oil emulsion is actually produced. This may be at the point where atomization takes place just prior or at the point of ignition. This, however, is not necessary, and the emulsion may be performed and conveyed to the burner nozzle in a preformed state. Particularly with the referred emulsions obtained by sonic agitation, the emulsion is quite stable and so it can be produced at a point remote from the actual burner itself, and such a modification is of course included. It is also possible to have the emulsion formed by flowing water and oil over the emulsifying point, so that the emulsion is formed at the same place, or practically at the same place, as atomization into the flame takes place. In the case of the use of sonic atomization, particularly for IC engine use, it is almost always preferable to have the streams of water and fuel unite just prior to the point of atomization. It is possible, of course, to feed to the sonic atomizer an already formed emulsion, but this requires a separate step and the results are not significantly better. Therefore, particularly in the case of sonic atomization for combustion, and even more particularly in the case of IC engines, it is generally preferred to have the emulsion formed at the point and as a part of the atomization or atomizing device.
It is an important advantage of the present invention that it is not necessary to use any emulsifying agent, particularly when sonic emulsification is used. This eliminates the added step and, therefore, cost of the emulsion is reduced, although in a broader aspect the present invention does not exclude an emulsion which has been made in the presence of a small amount of an emulsifying agent, such as a small amount, usually a fraction of a percent, of a dialkyl sulfosuccinate or other well known emulsifying agent capable of facilitating the formation of water-in-oil emulsions. The invention in this aspect, which is normally not preferred, may use any known emulsifying agent.
Ordinarily more problems are presented with the burning of heavy residual fuel oil, and this frequently requires steam heating. In the case of the present invention, however, the heavy oil emulsifies more readily than light oil, and when emulsified with a considerable amount of water, the viscosity is low enough so that it can be burned without preheating. This is an additional advantage for use with heavier oils. Why the heavy oil emulsifies more readily and to a lower viscosity has not been fully determined. It is possible that the heavy fuel oil contains contaminants which aid in the emulsification which are not present in the purer lighter fuel oils. It is not intended, however, to limit the present invention to any theory of action.
While, as has been stated, the invention is not limited to any particular method, sonic emulsification is greatly preferred. It produces emulsions of maximum fineness at very low costs, and so in one further aspect of the invention there is included the combination of forming ultrasonically a fine water-in-oil emulsion and then introducing this into a burner.
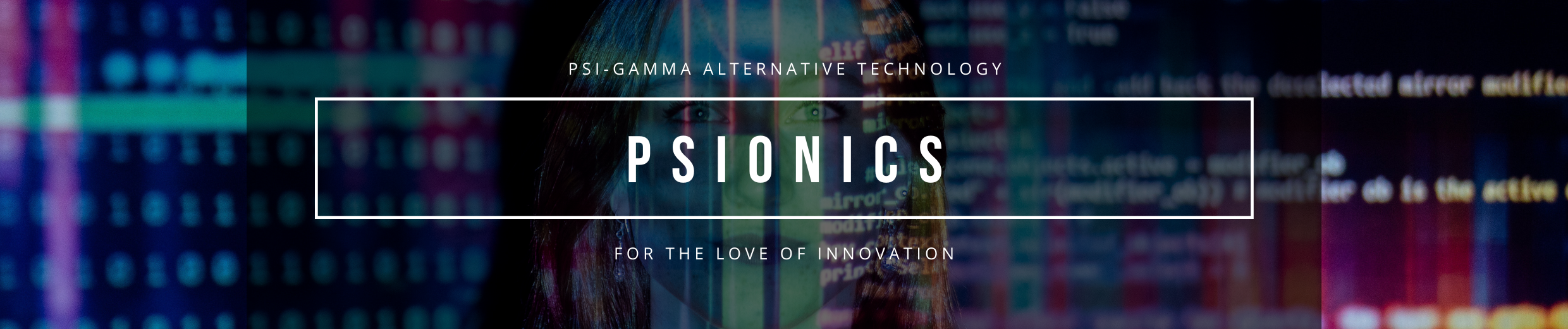
Эта статья для ознакомления предлагает читателям общее представление об актуальной теме. Мы стремимся представить ключевые факты и идеи, которые помогут читателям получить представление о предмете и решить, стоит ли углубляться в изучение.
Ознакомиться с деталями – https://quick-vyvod-iz-zapoya-1.ru/